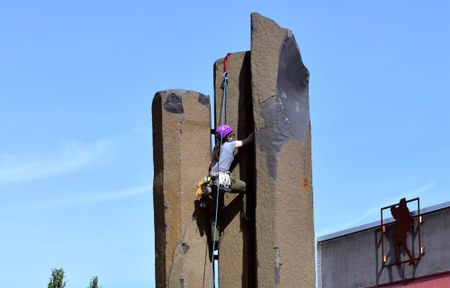
“The night before we didn’t sleep. We were seriously worried it’d be a disaster,” says John Ohlson, the man who hatched the idea of erecting 25-foot basalt columns at The Mountaineers Seattle Program Center.
Days earlier a batch of rock towers, weighing 15 tons each, arrived via semi-truck from a quarry near Moses Lake. John’s sleepless night came before the operation’s most delicate phase: hoisting the massive columns without breaking them (or killing someone in the process).
Although nerves were running high, the moment of truth came after years of meticulous planning. And if these rocks could talk, they’d tell you that their story began long before that:
The basalt hails from the Columbia Plateau, an area where pillared, rock outcroppings rise at a 90-degree angle from sagebrush-filled ravines. The striking geological formations trace back 17 million years to when lava flooded the area and crystalized into basalt rock. Researchers are still debating the specifics, but about 12,000 years ago, the colossal Glacial Lake Missoula floods came crashing west and carved out the rock walls we see today.
Several thousand years later, John Ohlson visited a petrified rock shop near Vantage and noticed a small basalt column out front. The shop owner pointed him to its quarry which he visited.
John later met with fellow volunteers Gene Yore and Glenn Eades to consider the columns for a climbing wall. “It had some real advantages,” John said. “Climbers could get a feel for real rock and practice placing cams and nuts in the cracks to catch their falls.” Gene, already serving as Seattle Climbing Chair, became convinced and stepped up as Project Manager with many volunteers helping out.
The benefits were undeniable, but as with many great ideas, the crew had to overcome a slew of logistical hurdles to turn their dream into a reality.
First they had to address what John describes as “crappy soil.” To support the columns, the team laid a 14x14x3-foot concrete foundation, with 32-foot steel pilings to provide an anchor. Like an iceberg, our basalt columns go further below the surface than above.
Then there was the quarry. John was amazed when he saw columns far taller than ours being plucked from the side of the rock wall by a high-powered excavator. The problem? The columns tended to break, which is okay for their primary use of being sliced into high-end floor tiles, but wouldn’t cut it for a climbing wall. The team found ten intact columns that looked like good candidates, but in the ensuing weeks five broke just sitting at the quarry.
Things didn’t get easier when it came time to bring them across the state. Within 20 miles of being loaded onto semi-trucks, another column broke. They were down to four, the minimum number needed. There was zero room for error.
With one crane holding the 15-ton column and another guiding it into place, the process of erecting the columns is an experience John describes as “pretty scary.” But when the two long steel prongs at the bottom of the first column met their corresponding holes in the concrete, John thought, “This might work after all.”
Indeed, it did. After their construction in 2011, John enjoyed following his son Dave’s lead on the first ascent, and the columns have been a wonderful training resource ever since. Rumor has it you can find a number of signatures of well-known Mountaineers in its summit register.
Note: Climbing the columns requires skill and caution. Metal bars connect the columns to one another. If climbing on the columns, do not grab, or place any climbing equipment on, these bars.
This article originally appeared in our Summer 2019 issue of Mountaineer Magazine. To view the original article in magazine form and read more stories from our publication, click here.
Add a comment
Log in to add comments.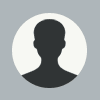
Great story, I've always wanted to know more about this. At one point, rumor had it that the columns shifted while the concrete was setting (?), leading to the crack widths being somewhat different than intended. Do you have any information to confirm or refute that?
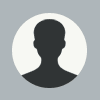
This is highly unlikely as the concrete was fully cured before the columns ever got near it. They may have shifted during the setting process, but probably in a minor way. There is much rebar in the base and it was connected to the pilings below. Prior to the columns being lifted and epoxied into place, the columns were lying horizontally and were analyzed dimensionally to determine where each would be located when erected and how they would be rotated and spaced with respect to each other. This was done so that several crack widths could be made relatively uniform. The columns were not perfectly straight so there is some variation with height. The bottom end of the columns was cut straight. The bottoms were drilled and the rebar was epoxied into the columns. A template of the bottom was made for each column including the location of the rebar sticking out. Once the design was made where each would be located and the angles, the templates were placed on the concrete base to locate where the holes for the rebar were to be drilled. Wooden blocks for the intended spacing were epoxied to the sides of the columns which were to face other columns. On erection day, the first column was placed and epoxied in place as vertically as we could given the uneven faces It was held by tilt-up building jacks on three sides.It was the reference for the rest of the columns. Each of the next columns was raised in place with the spacer blocks fixing the crack widths and held in place by more jacks. When all were in place the entire group was strapped together with trucker's cargo straps. Within a few days holes for the long threaded rods were drilled through the columns and epoxied which connected all columns together at two heights. When the rods were epoxied in place, a metal spacer matching the wood spacer thickness was placed on the rods in between the columns. The wood blocks were then removed. While there are small errors at each step and the columns are uneven, the crack widths were determined on the day of installation per the design. Then everything was stabilized by the horizontal rods. It is extremely unlikely that the crack widths have changed from the day of installation. The rock and 22 cubic yards of concrete plus all the steel give a solid structure. Minor settling could result in a slight tipping but would not affect the crack width.